이오테크닉스 사업
· 레이저응용장비 :
1) 반도체 : Marking, Cutting, Trimming, Stealth Dicing(좁은 Street Width가능, 미세소자컷팅=MEMS) , Grooving(TSV공정 홈 파내기)
2) PCB : Drilling(CO2, UV > PCB)
3) 디스플레이 : LLO(Laser Lift Off, Mother Glass제거), OLED Glass Cut(Mother Glass 제거)
*매출비중 : 반도체 > PCB > 디스플레이 > 2차전지
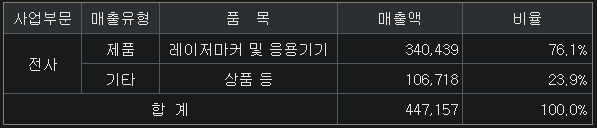
기회
· Marking, Annealing장비 광원 내재화 진행 중 > 원가절감 기대감
· 칩렛(Chiplet) 확산 중 > Marking(여러 개의 칩 명칭표기),
· PCB에 소자들어갈 구멍(Hole) 필요 > CO2 Drilling 사용 증가 > UV Drilling R&D
·
리스크
·
·
업데이트 :
주주구성(23.3월 기준) :
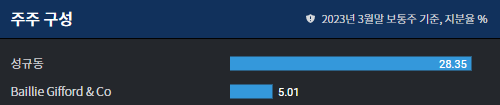
이오테크닉스
이오테크닉스의 이오(EO)는 Electro-Optics를 의미하는데요. 단어 그대로 전자광학기술을 다루는 업체라는 뜻이고 대표적인 예시가 레이저응용장비입니다. 동사는 레이저응용장비를 주로 반도체에 적용을 해왔는데요. Marking(글로벌 M/S 70%), Cutting을 주력으로 해오다가 점차 CO2 or UV Drilling(PCB에 적용), Annealing(Gap Filling=웨이퍼치료), Stealth Dicing(웨이퍼 Street Width 좁은 컷팅, MEMS 같은 미세소자 가공&세정 가능), Grooving(홈 생성, Low-k포함 고적층에 적합), LLO(Laser Lift Off, 마더글래스 제거) 등 포트폴리오를 다양화하고 있죠.
1. 레이저응용 > 반도체 :
1) Laser Marker :
강한 Laser가 표면에 닿으면 흔적이 남겠죠. 이 흔적을 디테일하게 남기면 Marking이 됩니다. 이러한 레이저의 특성으로 이오테크닉스는 웨이퍼, 칩, PKG 단계에서 제조사, 로고 등을 표시하는 Laser Marker를 만들어내고 있어요. 전 세계 M/S 70% 정도로 압도적인 1위 업체에요.
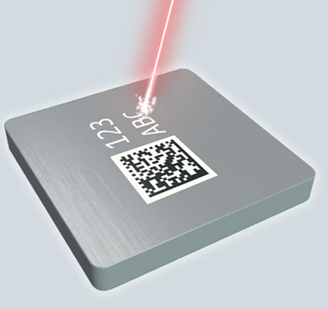
특히, 칩렛(Chiplet)구조가 요즘 주목을 받자 Marking의 중요성이 더욱 커졌는데요. 반도체는 원래 하나의 기능을 하는 칩만 따로 올렸었는데요. TSV(Through Silicon Via, 관통)기술이 나오자 다양한 기능을 하는 여러 개의 칩들을 모아보자라는 아이디어에서 나온 것을 의미해요. 여러 개의 칩이 한데 모이니 각각 이름을 표기해줘야겠죠. 그래서, Marking의 중요성이 Chiplet에서 커진겁니다.
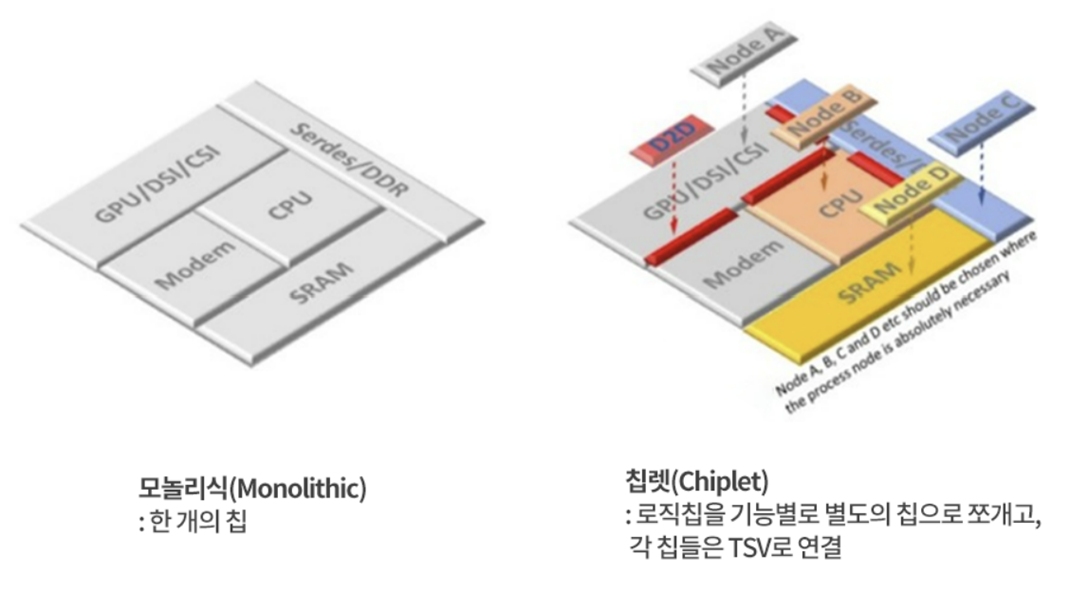
2) Stealth Dicing : 미세한 Dicing > 좁은 Street Width, 미세소자(ex-MEMS)
스텔스 다이싱(Stealth Dicing)은 레이저로 칩이 올라간 웨이퍼를 자르는(Dicing) 것인데요. Blade Dicing보다 수율, 속도, 접착강도면에서 뛰어나요. 스텔스 다이싱장비의 가장 큰 장점으로는 스트리트 폭(Street Width)를 줄일 수가 있어서 한 장의 웨이퍼에서 얻을 수 있는 칩의 개수가 증가한다는 것이에요. 전공정이 끝난 웨이퍼는 낱개의 칩으로 잘리는데, 칩 서로간의 간격을 스트리트(Street Width)라고 불러요. 건물 사이사이 길 처럼 생겼기 때문이죠. 스텔스 다이싱을 이용하면 보다 더 정밀한 컷팅이 가능하기 때문에, 기존 다이아몬드 다이싱보다 더 얇은 스트리트 간격으로 컷팅할 수 있어서 칩을 더 올릴 수 있는 장점이 있습니다.
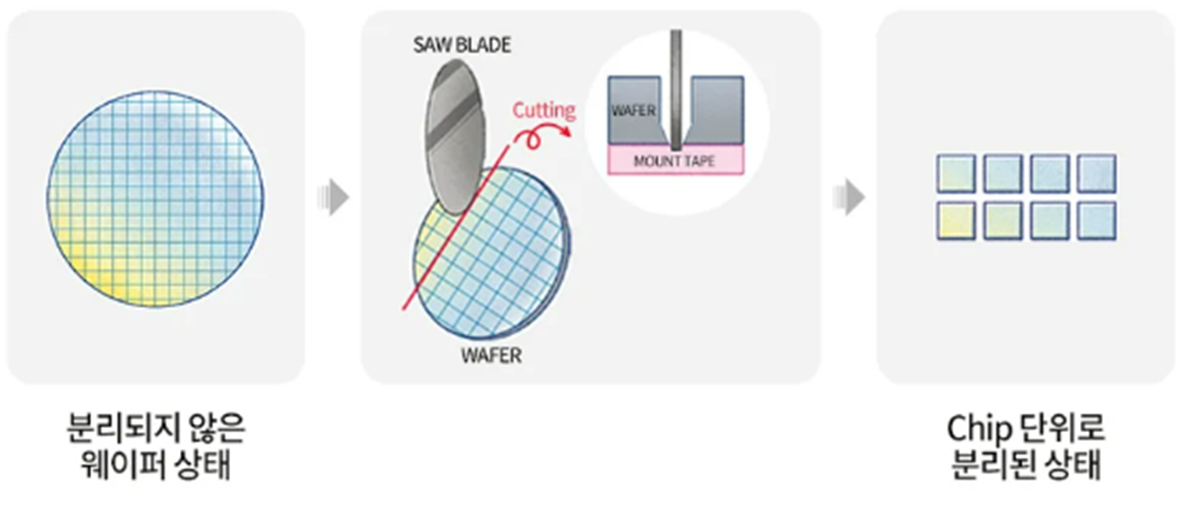
또한, 스텔스 다이싱은 복잡한 미세소자가 포함되어 있거나 예민한 칩 등에도 사용할 수 있는데요. 예를 들면, EDS공정에서 전기적 테스트에 쓰이는 프로브카드의 MEMS(Micro Electro Mechanical System)에 적용가능해요. MEMS는 프로브카드의 달려있는 작은 돌기 같은 것들로 이루어져있어요. MEMS가 웨이퍼 위 집적회로에 맞닿아 전기적검사를 하는 것이죠. 작고 가늘기 때문에 가공을 할 때 무척 취약합니다. 이때, 스텔스 다이싱을 사용을 해주면 MEMS에 데미지가 거의 안가죠. 참고로, 레이저로 가공+세정까지 해줍니다. 세정할 때 물을 사용하지 않고 레이저 자체로 세정하기 때문에(드라이 세정) 데미지가 가지 않는 것이죠.

3) Grooving장비 : TSV공정 홈을 파는 장비
Grooving은 홈을 파는 것을 의미하는데요. 특히, 점차 반도체PKG도 점차 고단화가 진행되면서 칩끼리 또는 PKG끼리 간섭현상을 막아주기 위해 Low-k를 증착하고 있죠. Low-k에 대한 자세한 설명은 'Low-k, High-k, 차이점 쉽게정리'를 참고해주세요. Low-k를 포함하여 실리콘 층도 있을 텐데 TSV(Through Silicon Via)기술이 들어가기 때문에 직선으로 홈을 내야하죠. 이때, Blade Dicing으로 홈을 내면 직접 소자층에 닿기 때문에 결함(Defect)이 생긴다거나 박리(Delamination) 현상이 발생을 할 수 있죠. 그래서, 레이저를 이용한 Grooving 장비가 주목받고 있어요. 다만, 일본 Disco사가 거의 독점하다시피 하고 있기 때문에 시장진입은 지켜봐야할 것 같아요.
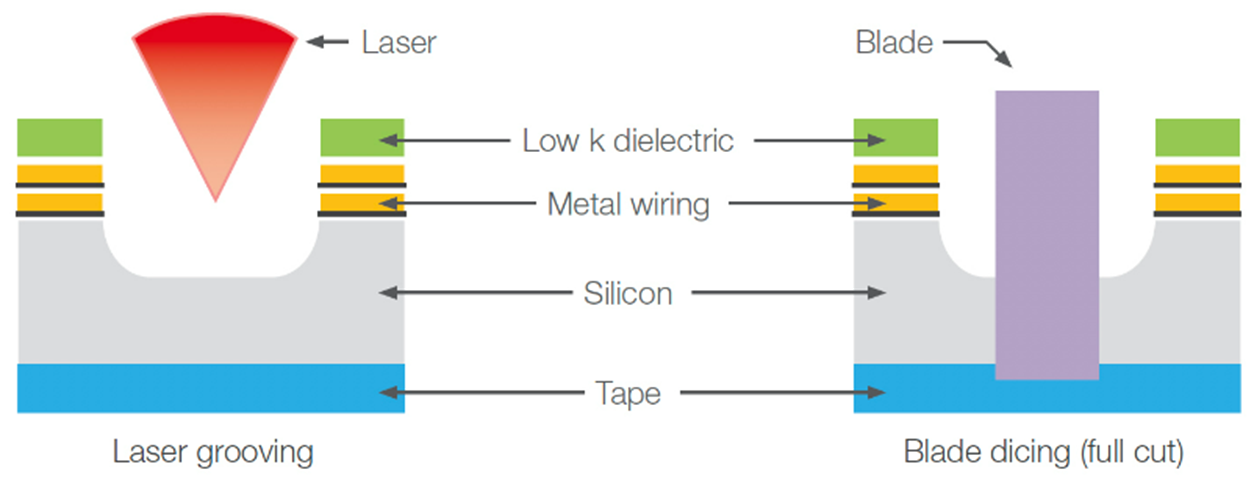
2. PCB(Printed Circuit Board, 인쇄회로기판) : CO2 Drilling, UV Drilling
CPU, GPU, AP가 두뇌역할을 한다면, PCB(Printed Circuit Board)는 두뇌의 명령을 전달하는 신경망 역할을 하죠. 칩이 내리는 명령을 전달 받기 위해서는 칩과 PCB가 접촉이 되어야하는데요. 그러기 위해서는 구멍을 뚫어서 결합부위를 만들어줘야겠죠. 즉, Drilling이 필요한 것입니다. 이오테크닉스는 강한 CO2를 이용하여 Drilling을 하는데요. 다만, 미세화 능력과 경화작업이 빨리 되지 않는다는 한계가 있어요. 그래서, UV를 이용한 UV Drilling 장비를 개발했습니다. 더 강한 에너지로 구멍을 뚫기 때문에 속도도 빠르고 CO2 배출도 현저히 줄어들었죠.
3. 디스플레이 : LLO, OLED Glass Cut
레이저응용장비는 앞서 살펴본 반도체 뿐만 아니라 디스플레이에도 쓰여요. 대표적으로 LLO, OLED Glass Cut장비가 있죠. LLO는 Laser Lift Off의 약자로 말 그대로 레이저(Laser)로 들어올려서(Lift) 떼어내는(Off) 것인데요. OLED 처럼 디스플레이가 백라이트, 편광판, 컬러필터가 필요없어지자 두께가 상당히 얇아졌죠. 얇아진 만큼 제조공정도 어려움을 겪고 있는데요. 특히, OLED 처럼 가느다라고 완전히 평평함을 유지해야함과 동시에 디스플레이를 만들어야하기 때문에 깨질 위험이 있어요. 그래서, 마더글래스(Mother Glass or Glass Substrate)라는 보호막을 먼저 깔아주고 그 위에 폴리이미드(Polyimid, Flexible 적용시)를 얹는 식인 것이죠. 마더글래스는 애초에 디스플레이를 아래에서 보호목적이었으니 마지막에는 제거를 해줘야겠죠. 이때, LLO장비가 쓰이는 것이에요. 아래 그림에서 '유리판 제거'공정에 해당합니다. 참고로, OLED Glass Cut 장비도 사용이 됩니다.

4. 2차전지 : Laser Notching
레이저는 2차전지공정에서도 쓰여요. 특히, Cutting에 레이저는 특화되어있기 때문에 2차전지전극을 자르는데 주로 쓰이고 있는데요. 정확히는 파우치용 전극의 Notching장비로 쓰이고 있습니다. 2차전지는 전극공정-조립공정-활성화공정으로 이루어져 있는데요. 제가 포스팅한, '2차전지공정, 3분만에 정리'를 보고 투자아이디어를 얻길 바랍니다.
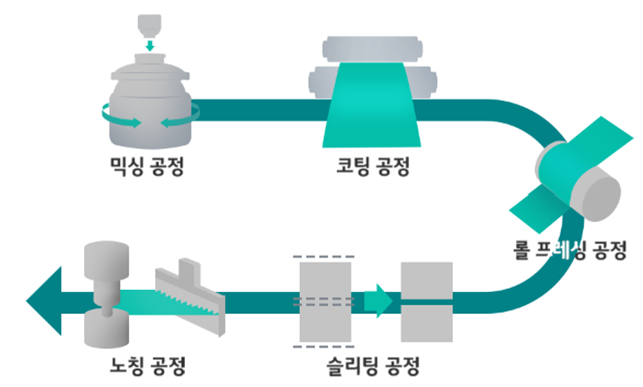
연구실적으로 보는 이오테크닉스의 현 주소 :
개인적으로 이오테크닉스의 연구실적과 연구계획을 보면 동사의 현 상황과 미래 비전이 보인다고 생각을 하는데요. 같이 몇 개만 살펴볼까요.
반도체는 보통 칩(Die)-기판(Substrate)-보드(PCB) 연결로 만들었었는데요. 기판이 중간다리 역할을 그동안 해온 것이죠. 하지만, 점차 반도체의 초미세화와 더 빠른 전자이동성이 현실화되면서 기판을 제거한 칩-보드 형식으로 바뀌고 있어요. 즉, 웨이퍼(칩이 올라가 있는 상태)에서 바로 PCB와 결합하여 패키징을 진행하는 것이죠. 이를 WLP(Wafer Level Packaging)이라 부릅니다. 그러면, Marking도 기판이 아닌 웨이퍼레벨에서 진행을 해야겠죠. 아래 R&D 실적을 보면, WLP 레이저 마킹시스템을 개발한 것으로 나와있습니다.


이오테크닉스에 대한 지속적인 업데이트는 맨 위 상단을 참고하면 유익합니다 :)
'반도체_후공정장비 > TSV(HMB, 3D낸드 필수)' 카테고리의 다른 글
한미반도체, 후공정 99% 장비 모두 공급하기 때문에 가치가 높습니다(쉽게설명!!) (0) | 2023.04.26 |
---|